This coverage of deck equipment focuses almost exclusively on winches, starting with what might be called a “one-of-a-kind winch.” That’s followed by another unusual winch, then a more conventional winch, and finally by how to ensure your winch (or winches) can be relied on.
Up first is a traction winch from MacGregor (part of Cargotec Corp.).
Fin Moore, sales manager at MacGregor, emphasized how different the winch is by labeling it “a one-of-a-kind winch in the world.” Actually, it’s not a one winch deal but 36 traction-winch systems with 72 storage reel brakes that will go on the Armor 1, a 180'×75' concrete mat sinking barge being built at Thoma-Sea Marine Constructors, Houma, La.
The Army Corp of Engineers will operate the Armor 1 along the Mississippi River, replacing a barge that has been in operation since the 1940s. The Armor 1 should be in operation by mid-2022.
MacGregor’s traction winches on the Armor 1 are to be part of a robotic crane gantry system headed up by SIA Solutions LLC that’s designed to launch into the Mississippi concrete mattresses made up of rows of concrete blocks wired together. The concrete mattresses shield the riverbank from erosion, ensuring safe navigation.
The traction winches and robotic gantries replace a system that relied on intensive manual labor and older winches where all the drums were on a single shaft. “With the new barge there will be 36 individual winches all wired into an overall PLC control system,” said Moore.
The winch lines, which Moore describes as being “consumable,” help tie together the concrete blocks that are wired together to form the concrete mattress. They are released into the river from the Armor 1’s angled side, which makes it easier to launch the mats, starting near the shore then moving farther out into the river. The winch lines go with the mattress and stay with it. Once the line on one drum has been used, the drum is replaced with another line drum.
The winches have an electric drive programmed into the overall robotics PLC control system so the back tension on the line can be controlled and the line doesn’t go slack as it goes out.
SCHOELLHORN-ALBRECHT
The 495'×72' ATB barge Commander, pushed by the tug Bradshaw McKee, left Fincantieri Bay Shipbuilding in late 2018 after she underwent an extensive conversion. The former self-unloading bulk carrier was converted to a self-unloading cement carrier.
At the Sturgeon Bay, Wis., shipyard, the freight barge was lengthened from 350', received new cargo holds, trunk deck and bow, and a new cargo unloading system.
In addition, six new Schoellhorn-Albrecht Machine Co. SW-100-50E mooring winches were installed on the Commander’s deck, three on the starboard side, three to port. “They replaced all their winches with ours,” said Brian Pavlisin, president of Schoellhorn-Albrecht in St. Louis.
What makes the SW-100-50E winch different from most mooring winches is the “auto” or unattended mode feature that provides constant line tension in mooring applications without anyone operating the winch. The mooring line automatically pays out or hauls back, keeping the vessel tight to the dock as cargo is being loaded, unloaded or as the tide changes. “The uniqueness is in the variable frequency drive and the controls we have integrated into the winch. The winch is smart. It knows when to pay out and pay in,” said Pavlisin.
With the winch automatically paying out or hauling in, the crew doesn’t have to worry about continuously adjusting mooring lines. That frees them up for other work. Also, because they don’t have to be around the winches and the mooring lines, deck safety is enhanced. “It’s a smarter way to handle the operations of the winch,” said Pavlisin.
The winches on the Commander are powered by 50-hp electric motors and are capable of a continuous line pull of 15,000 lbs. at up to 100' per minute. There’s storage capacity for 600' of 7/8" to 1-1/8" wire rope, and the tension is adjustable between 0% and 100% of the rated line pull.
The winches can be controlled from a multibutton control panel, mounted on a pedestal, one on each side of the Commander. The pedestals communicate with each other and a single pedestal can control one or multiple winches paying out on one side of the Commander when needed, while other winches compensate for the tension by paying out or hauling in.
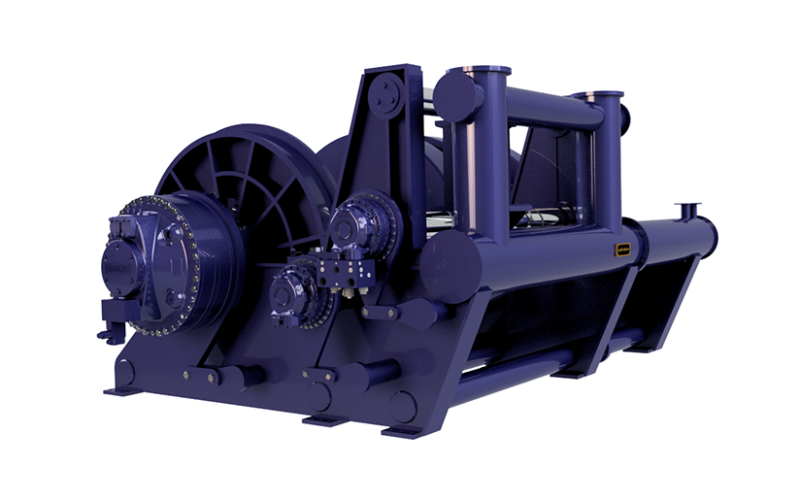
JONRIE
JonRie’s new Series 525 double-drum towing and escort winch was designed for a 6,770-hp ASD Rotortug for Seabulk Towing. The towing drum has 100,000 lbs. of line pull and a drum capacity of 2,000' of 2 1/2" wire. The escort winch has a maximum line pull of 50,000 lbs. and a drum capacity of 600' of 8.5" hawser.
A difference between this winch and the last Series 525 winch is four independent Hägglunds motors: one each on the towing and escort drums, and one each on the levelwind and gypsy head. The direct-drive Hägglunds motors on the levelwind and gypsy head “are brand new to (Hägglunds) and called a CAB,” said JonRie’s Brandon Durar.
He said the Hägglunds CAB is “a great advantage on the gypsy side.” With the old planetary gearbox, “if you overcome the brake with a load on the gypsy, it tends to break the gearbox. In another words, it’s light duty. This device is heavy duty,” and instead of having both a motor and a gearbox, there’s just a motor.
One other feature: you don’t have to leave the pilothouse and go on deck to adjust the level wind. “It’s all done from inside the wheelhouse. You don’t have to go to the deck to declutch,” said Durar. “We were the first ones to do that.”
Another new feature is when the winch isn’t engaged and is in neutral “the block opens and the two motor ports communicate. If you have any kind of side load on the levelwind the motor will spin backwards and you are not going to break anything,” said Durar.
In early July, the first winch had been delivered and the second winch will be delivered around Christmas.
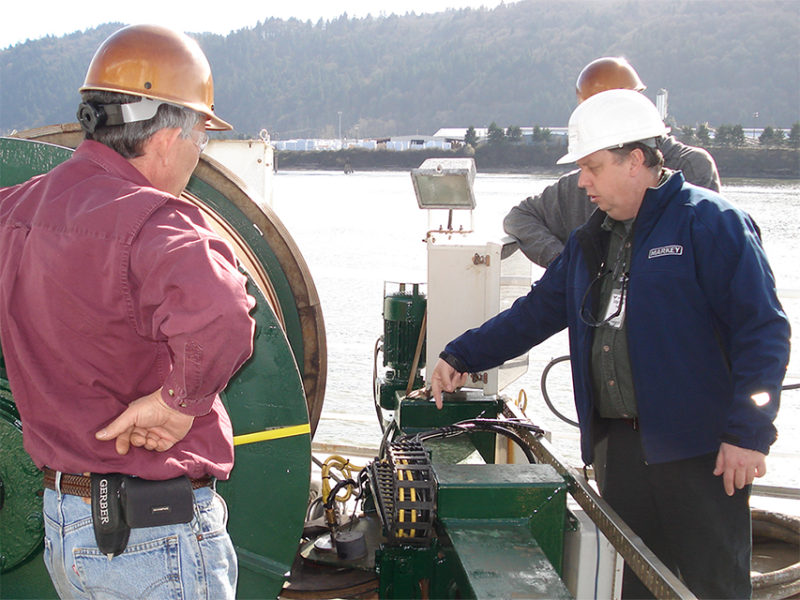
MARKEY MACHINERY
Imagine that last week your tug had to be pulled off a ship-assist job at the last minute and docked at the local shipyard because of a problem with the deck winch. This kind of unplanned, urgent maintenance is not good for a tug company’s business.
Better to think in terms of long-term preventive deck-equipment maintenance, which is what Markey Machinery offers with its Sentinel Maritime Safeguard & Inspection program. It was introduced about two years ago, after the Coast Guard came out with Subchapter M, which “identified deck equipment winches as critical equipment for a tugboat. It became a more important thing in the eyes of the Coast Guard to make sure you have reliable deck equipment,” said Scott Kreis, Markey Machinery’s vice president.
Markey’s Sentinel Maritime survey program basically evaluates the condition and readiness of a vessel’s deck equipment. The survey is designed to be a checklist for deck equipment specific to your tug. “Whatever winch you have we will develop that checklist,” said Kreis. It can be for a Markey winch or one from another manufacturer.
Most of the time the checklist consists of “300 to 400 points to check,” though sometimes there have been 1,000 points to examine. Included in the survey are hydraulic, electrical and mechanical systems, as well as a vibration analysis that’s done shaft line by shaft line.
On older winches, the survey also identifies components that are obsolete, “then we have to figure out what components we can get that will serve the same function. We try to stay ahead of obsolescence,” said Kreis.
The cost of the survey consists of travel time to the vessel for one or two technicians — one for mechanical systems one for electrical — when several pieces of equipment need to be examined. Markey’s technicians have traveled from Seattle to Hawaii, the Gulf of Mexico and up and down the West Coast to do surveys.
The best time to conduct a survey is prior to drydocking. Then the survey “spells out some areas to pay attention to during the drydocking but also gives replacement part quotes and service quotes,” Kreis said.