Diesel fuel and sludge formations aren’t good buddies The result of that combination is clogged fuel lines and higher-than-normal filter replacement while giving you and your boat a reputation for undesirable exhaust emissions.
When things get really bad some companies with larger vessels must have their fuel tanks manually cleaned every couple of years to remove the bacterial infections and sludge
Matching your fuel system up with the right fuel additive can avoid such a scenario. It certainly hasn’t been a problem for the vessels of a large coal company in Hong Kong that has been adding Fuel Right’s fuel additives to its vessels’ diesel fuel for the past five or six years. All the vessels are within the 50,000- to 78,000-dwt category and transport coal to major Chinese ports.
The fuel additives “purifies the fuel lines and tanks and achieves about a 3.5 percent savings in fuel,” said Carl Magnell of Wilmington, Del.-based Fuel Right. Fuel Right works by depositing a microscopic coating inside fuel tanks, fuel lines, filters, and strainers, which protects the system from corrosion, even when there are contaminants and water present.
Fuel Right was brought into use on the coal ships on a trial basis in 2016. After showing significant improvements in cleaner filters, fuel viscosity, and reduced emissions (as well as fuel economy), Fuel Right additives are now used in 43 of the coal company’s vessels, for a $5 million to $6 million annual fuel savings, according to Fuel Right.
Another test of the benefits of using Fuel Right’s additives took place without Fuel Right’s initial knowledge, said Magnell. It was by the operators of the tug Naomi Princess that had just been built in China and was being delivered to Lagos, Nigeria, for oil field work. That’s a distance of 8,218 miles divided into two legs: China to Singapore (3,366 miles) and Singapore to Lagos, Nigeria (4,852 miles), where it would work in Nigerian oil fields. The run from China to Singapore took 15 days. It was made without Fuel Right, at an average speed of 9.78 knots, burning 5.62 metric tons a day in light to moderate sea conditions.
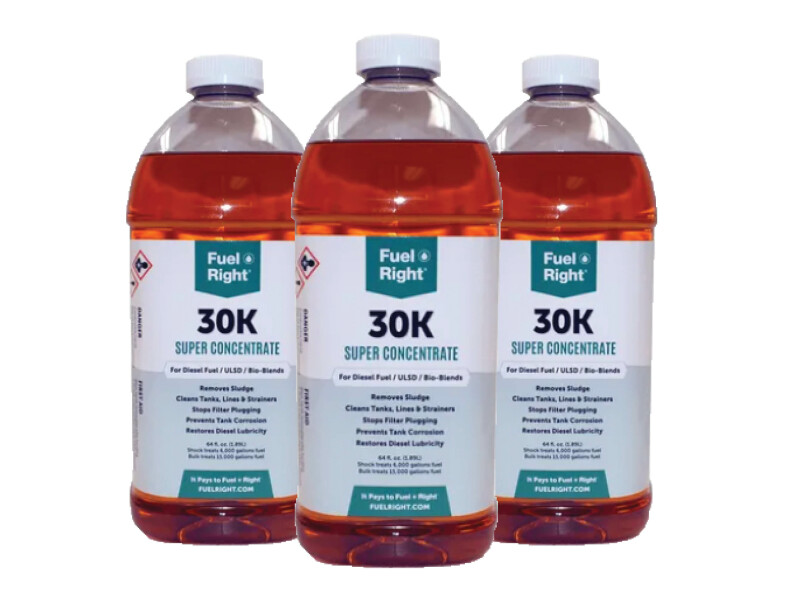
Fuel Right 30K was added for the second leg, from Singapore to Lagos. That trip took 22 days at an average speed of 9.5 knots while burning 5.03 metric tons a day in moderate to rough sea conditions. Overall, there was a “one metric ton of MGO fuel savings per day and no visible emissions,” according to the tug’s chief engineer, as quoted on Fuel Right’s website.
Magnell emphasizes that Fuel Right not only reduces the amount of fuel burned, but “the other significant thing we do is reduce emissions.” That would be about 60% hydrocarbon emissions and 38% particulate emissions. That’s based on an independent study by the faculty of Naval Architecture and Ocean Engineering at Istanbul Technical University.
INCIDENTAL DISCHARGES
In 2018, the Vessel Incidental Discharge Act (VIDA) went into effect, establishing new standards for vessel discharges incidental to normal operations. That did not include deck equipment, but with its potential for above-water discharges, deck equipment has become a focus of the Environmental Protection Agency. That includes lubricant discharges from machinery such as booms, jibs, and cables extended over the side of a boat as well as lubricants that leak onto the deck and are then washed overboard.
Thus “there’s the possibility of including deck equipment” under VIDA regulations, said Brandon Richards, Panolin America’s CEO. If that happens VIDA will be expanded beyond the oil-to-sea interfaces found with marine gear such as thrusters, stabilizers and rudders.
The likelihood that deck equipment will be included in the next iteration of VIDA is driving the growth of environmentally acceptable lubricants (EALs). The lubricants would need to meet three criteria, according to a proposed VIDA ruling: they must be “biodegradable, minimally toxic and not bioaccumulative.” The “use of EALs is basically growing,” said Richards, noting that “biodegradable lubricants are our (Panolin’s) niche.”
That “niche” might explain why Panolin is the only company to have its environmentally acceptable hydraulic fluids gain approval from the Bosch Rexroth Fluid Ratings List, which, after extended testing, recommends the best fluid solutions for individual application types against international standards.
To meet the growing demand for EALs, Panolin introduced a new product line, HLP SYNTH E. (The “E” stands for eco-label, indicating it conforms to environmental standards.)
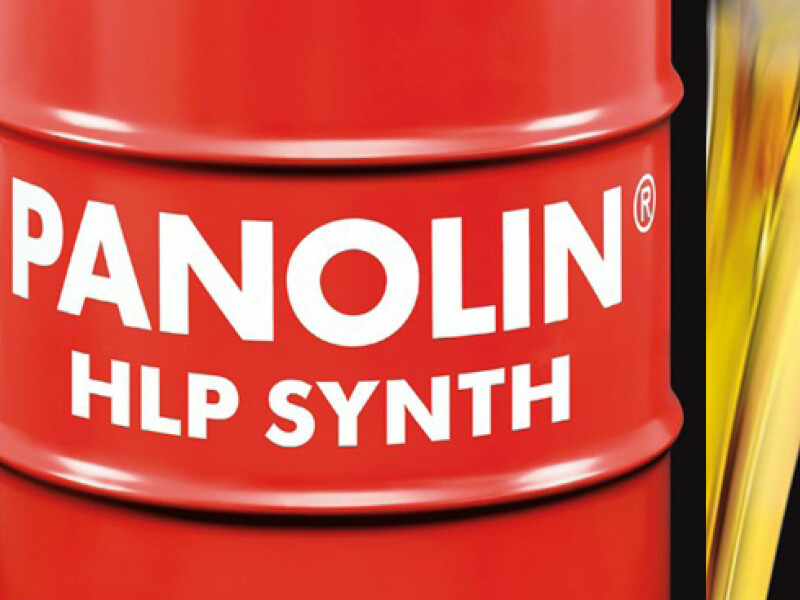
Panolin’s HLP SYNTH E is a synthetic, biodegradable hydraulic fluid of saturated organic compounds, called esters, with special additives. It’s designed to prevent the formations of deposits and gumming, even at high operating temperatures. The new bio-hydraulic fluid is fully compatible and mixable with Panolin HLP SYNTH and is available in various viscosities, including 15, 22, 32, 46, and 68. It complies with the European Ecolabel and VIDA/VGP.
Richards acknowledges that saturated esters “are the most expensive,” but at the same time, he said, “they are the most reliable and highest performance.” Still, vessel operators that aren’t familiar with different types of biodegradable oils “are often making a decision on price.” That may mean using a product that compromises their equipment and turns into a leak, which may cause an oil spill.
That could be the case with vegetable-based or unsaturated oils when they heat up in a hydraulic system and start “cooking,” Richards said. “You get varnish and shellac and clogging of filters, but the price point is a lot lower,” he said. Though there’s a savings on the upfront cost, “they pay more for the equipment failures and downtime.”
In contrast, EALs such as those from Panolin are specifically designed to avoid such issues.