Inadequate planning for “hot work” steel cutting and welding led to a February 2021 fire aboard a commercial fish processor while docked at a shipyard in Tacoma, Wash., the National Transportation Safety Board says in a new marine investigation report.
The 233' Aleutian Falcon was in the shipyard for maintenance and repairs in preparation for the 2021 processing season when a fire smoldered for hours after steel-cutting work was completed for the day. The fire broke out and was reported by a passing driver around 10:30 p.m. Feb. 17, 2021, when no one was aboard the vessel.
The Tacoma Fire Department responded, but the fire was not fully extinguished until four days later. There were no injuries, and an estimated 20-30 gallons of hydraulic oil that leaked into the water were captured by a containment boom. The vessel was declared a total loss with an estimated value of nearly $16.5 million.
Built in 1981 as an offshore support vessel by Halter Marine in Chickasaw, Ala., and originally named the Petromar Falcon, the Aleutian Falcon was renamed and converted to process Alaska cod and salmon at the Bender Shipbuilding and Repair Company of Mobile, Ala., in 1988.
In 2004 the vessel was acquired by Trident Seafoods, and since then served during the spring-summer season – also serving after the season as a bunkhouse for workers at the Trident processing plant at Akutan in the Aleutian Islands.
The February 2017 maintenance and repair schedule called for replacing a section of corroded steel plating, located on the bridge deck above the pantry, dry stores area and walk-in refrigerator, to be cropped and renewed. Considered “hot work” because oxy-acetylene cutting torches and electric grinders with cutting wheels can produce sparks, the first steps would be followed by fitting and welding new steel plate.
Under safety protocols, a marine chemist was brought on board to examine the areas involved. The marine chemist issued a certificate stipulating that the steel work had to be completed “without penetrating” the bridge deck, “indicating he either was not aware or clearly informed of the full scope of the planned hot work, or he wrote the stipulation in error,” according to the NTSB.
The certificate required all foam insulation within 12 inches of the area of planned hot work to be removed, and workers told investigators that they removed the foam insulation in the area of hot work.
“However, they did not remove a foam-filled wooden bulkhead separating the walk-in refrigerator space, adjacent to the pantry, which was combustible,” according to the NTSB. “The fire most likely started near the wooden bulkhead, located directly below the area where hot work had been completed for the day. The hot work would have produced sparks and slag that likely travelled from the deck above (overhead) down to the wooden bulkhead, igniting the combustible materials in the area, as well as the bulkhead, and allowing for a smoldering fire to become established.”
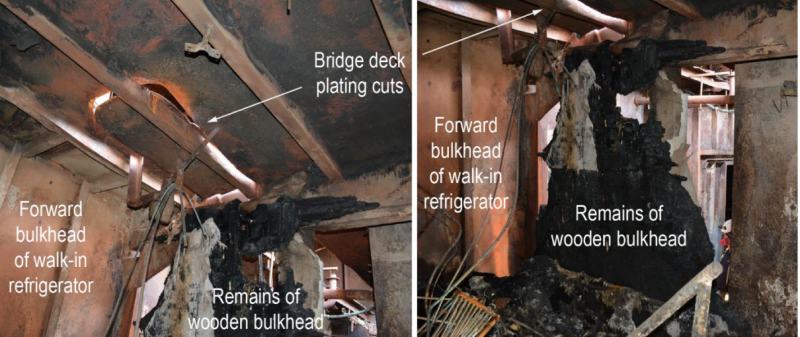
The agency’s report discusses apparent miscommunication before the repair work began.
While the marine chemist told investigators that cutting through the bridge deck was not discussed, the port engineer stated the intent was to cut away and insert new plating in the deck, the report notes.
On Feb. 17 the work crew included a supervisory lead welder, four welders, one laborer, and four fire watches, who told investigators how they removed polyurethane foam insulation and protective paint coatings near the planned hot work and protected all combustible materials that could not be removed with fire blankets and fire suppression gel.
Where flammable materials could not be removed, fire blankets would be used to cover the area and jammed into cracks, then wetted.
The report notes how those preparations were verified by walk-through before a welder in the dry stores area began cutting the deck plate with a cutting torch at 12:30 p.m., to free plating from the frames below by burning through welds.
Fire watches were assigned to monitor the hot work areas, including the pantry, dry stores area, and walk-in refrigerator. During the plate cutting and freeing a small fire ignited in a piece of plywood located in the dry stores area, which was put out by the workers before they continued work.
All cutting work was completed around 3:20 p.m., and the fire watch was the last worker to leave that area of the vessel around 4:30 p.m. A security guard working that evening saw nothing happening.
At 9:45 p.m. a motorist noticed white smoke coming from the vessel, but believed it was ongoing shipyard work. Further along the road, he stopped again, saw an orange glow on the Aleutian Falcon and called to report the fire.
The NTSB found inadequate planning for the steel work led to the fire.
“The NTSB determined the probable cause of the fire was the company’s supervisory personnel inadequately planning for hot work, as well as shoreside workers’ inadequately protecting hot work areas, allowing slag from hot work to ignite combustible material near an insulated wooden bulkhead of a walk-in refrigerator that had not been removed or sufficiently protected. Contributing was the ineffective communication between the supervisory personnel, marine chemist, and workers.
“It is critical for supervisory personnel to evaluate hot work areas for fire hazards to ensure that effected spaces are completely understood, prepared and protected for planned hot work in accordance with regulatory guidelines, company policies and marine chemist certificates,” the report said. “Adherence to proper policies and procedures is vital to completing a safe hot work operation. Additionally, crewmembers and personnel involved in hot work should be able to identify hazards and take action to remove or mitigate potential risks to the vessel.”
In earlier cases the NTSB likewise faulted hot work planning for fires on other vessels in recent years: An August 2016 fire aboard the passenger vessel Tahoe Queen, the May 2018 fire aboard the cargo ship Chipolbrok Moon and the December 2018 fire aboard the fishing vessel Jeanette. In all three cases the board found hot work safety policies were not followed.