Aharbinger of shifts in propulsion engine technology for the workboat market took place in May, almost a year ago. That’s when a pair of MAN 1,019-hp D2862 LE428 12-cylinder diesels that had been modified to run on a dual-fuel combination of hydrogen and diesel went into the 82'×24'×6' Hydrocat 48, a crew transfer vessel operated by Vestes, a Danish offshore wind company.
“It’s a very cool kind of benchmark project that is a test for new technology to save a lot of carbon emissions,” said Jason Blume, MAN Engines & Components sales manager in Pompano Beach, Fla. What seems a bit counterintuitive is the dual-fuel operation utilizes a conventional MAN V12 marine engine that doesn’t need to be optimized for hydrogen. It only requires the hydrogen injection system developed by the Belgian engineering firm CMB.TECH.
In the dual-fuel hydrogen-diesel mode, a measured amount of hydrogen is injected into the charge air that’s then ignited with diesel fuel in the cylinder’s combustion chamber. That combination, even when running at full load, releases less CO2 in the exhaust gases than when running on straight diesel. “The sweet spot” for fuel consumption is between 1,700 and 1,900 rpm, said Josie Hollingsworth, MAN’s sales manager for marine engines. At that point the engine is burning about 80% hydrogen and 20% diesel.
If the hydrogen tank runs empty or a problem develops with the hydrogen system, the engines switch back to being powered solely with diesel fuel and utilize selective catalytic reduction (SCR) aftertreatment systems to clean the exhaust. The two dual-fuel engines give the Hydrocat 48 a maximum speed of 37 mph, a service speed of 34.5 mph, and a bollard pull of 12.8 tons.
Blume said there’s not much of a learning curve for MAN’s dual-fuel engine. The operation is “seamless, no matter what fuel it’s running,” he said. “It will automatically inject hydrogen when it can and run in dual-fuel mode, without operator input.” If there is a learning curve and one that requires a certain expertise, it would be for boatyards installing a hydrogen fuel storage system in a vessel. That’s because the hydrogen needs to be in liquid form to give it the required amount of density. “It must be kept quite cold, about minus 250 degrees Celsius,” said Hollingsworth.
The hydrogen system has a couple of built-in risk mitigation components. For example, when hydrogen leaves the storage tanks, it flows through a low-pressure system of double-walled piping. The low-pressure system “is much less likely to have leaks,” noted Blume, and the piping being doubled-walled, it’s highly unlikely that both walls would be penetrated.
Currently, the MAN dual-fuel engines aren’t sold in the U.S. The engines have only IMO Tier III approval. However, Hollingsworth said certification for the U.S. market is ongoing, and she expects to have EPA Tier 4 certification in 2024. In the long run, based on the work developing the dual-fuel engines, it’s possible that the next step for MAN or another engine manufacturer will be a fully hydrogen-powered vessel.
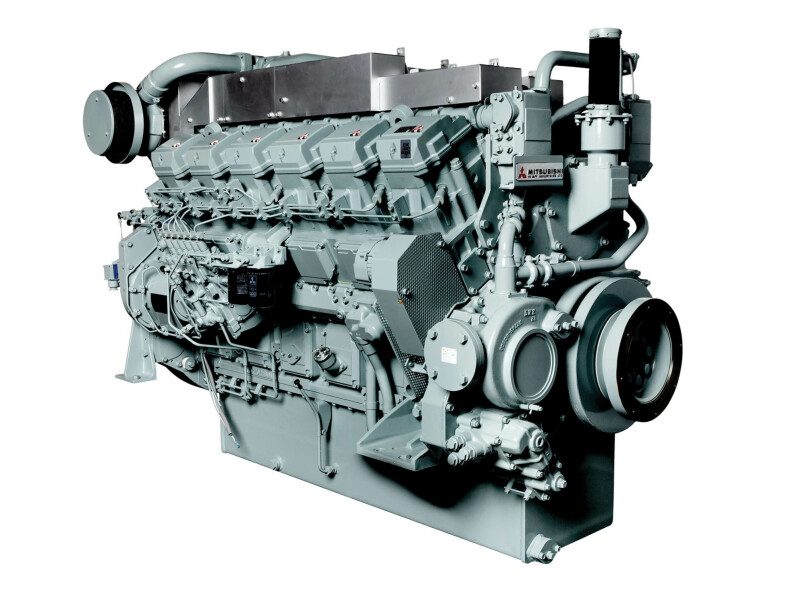
MITSUBISHI
The market for Mitsubishi’s newest engine offering, the Tier 3 S12R with a 1,100-hp rating at 1,800 rpm, is very focused. Mitsubishi’s S12R is not designed for newbuilds. It’s designed for workboat operators interested in repowering to move older vessels from Tier 1- or Tier 2-rated engines to the cleaner burning Tier 3 level. A major market is twin-screw, 2,000-hp inland towboats, as well as tugboats.
The original Mitsubishi S12R was introduced some 20 years ago with a 1,600-rpm rating. The newest version, which was introduced this January and has an 1,800-rpm Tier 3 rating, “makes it easier for operators to repower older vessels that were running at 1,800 rpm without making gear or propeller modifications,” said Trace Laborde, vice president of sales at Laborde Products Inc., a Mitsubishi distributor, based in Covington, La.
Laborde also noted that most older workboats have mechanical engines, meaning fuel flow is metered by an injection pump, and Mitsubishi engines are mechanical. Most of the vessels that Laborde expects the Mitsubishi S12R to repower are already set up for a mechanically controlled diesel. “The crews are familiar with it, and they like it because it’s less complicated and more service friendly” than electronically controlled engines, said Laborde. In fact, Mitsubishi Marine engines are the only Tier 3 mechanical diesel engines in the workboat market, according to Mitsubishi.
The Mitsubishi S12R weighs in a bit heavier than some of its competition at 11,731 lbs. for 1,100 hp. That might be a concern if the intent was to repower a high-speed or relatively high-speed workboat, but for vessels such as towboats and tugboats, the engine’s weight “does not affect fuel consumption,” said Laborde. “These are displacement-hull vessels. They don’t need to go fast, and that’s the right application for a Mitsubishi engine.”
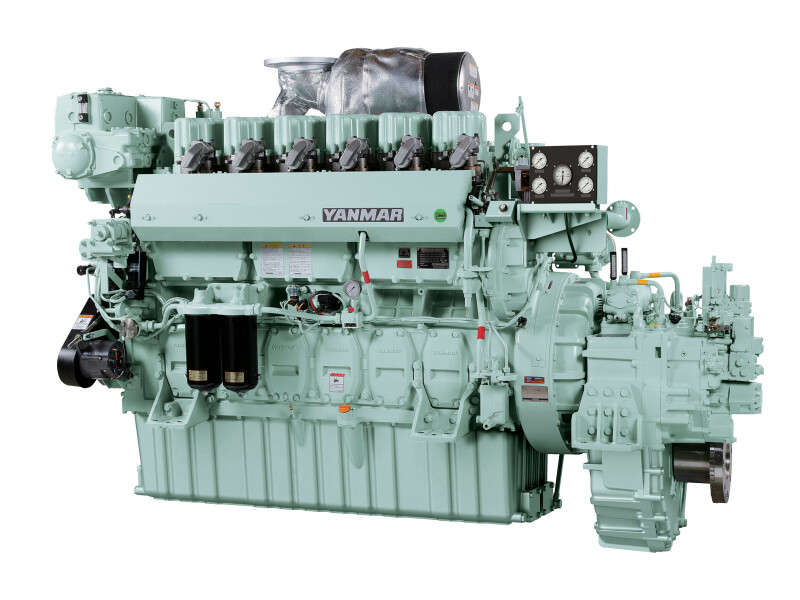
YANMAR
Workboat operators with vessels based in Canada now have the option of a new Yanmar engine model with an SCR system that allows it to meet IMO Marpol Tier III emissions requirements for nitrous oxides, or NOx. It’s the 6EY17WS, an in-line six-cylinder engine based on the existing 6EY17W engine, with a horsepower range of 501 to 1,122. (If sold in the U.S., it would have to meet Tier 4 requirements, but not in Canada.) The SCR system, which is a Yanmar product designed for Yanmar engines, reduces NOx emissions by about 80% compared with IMO’s Tier I standards, said Nathan Stabler, a senior marine engineer at Yanmar America.
Yanmar’s new engine is available with Yanmar gearboxes with ratios from 2.5:1 to 5:1. The first Yanmar 6EY17WS is going into a 73' crabber due to be launched next spring in New Brunswick, Canada. That’s to be followed by a second vessel in August and a third in spring 2024.