Four decades of running fleets and a shipyard will teach you to spend money upfront and avoid more pain later, said Arlen “Benny” Cenac Jr.
“The most important thing to us is ‘What will keep that boat afloat?’” said Cenac, the third-generation owner of Cenac Marine Services-Main Iron Works based in Houma, La.
“Too many people own boats with patches on the bottom, with tubes leaking like crazy. Those days have been gone for us by 40 years,” Cenac told the audience at the 40th annual International WorkBoat Show Maintenance and Repair Program in New Orleans Wednesday.
“Good communications on the maintenance side of the vessel” is critical to success,” Cenac stressed. It establishes security for the crews, “so they go off watch they know they are on a safe vessel," he said.
When the boat goes into drydock, conversations and visits by the boat captain, the owners’ captain of the port and shipyard manager establish common understanding of the boat’s issues and needs, said Cenac.
“Not to brag, but I think we were way ahead on this Sub M thing,” said Cenac of the Coast Guard’s sweeping safety requirements for towing vessels. “We do detailed workups of what that boat needs and how to get it done.”
Cenac ticked off his longtime punch list of what to check: cooler boxes, stuffing boxes, bladder seals, wear and tear on the bottom of the hull.
Worn steel can be a hazard in a future grounding, said Cenac. The nuisance of ropes in the wheel can pose long-term danger to the propeller shaft and coupling if they are not carefully inspected, or “that boat will sink in a heartbeat,” he said.
Following Cenac’s presentation, David Kober, senior sales engineer for IBA America, talked about the ongoing digital transformation of maintenance and repair – the technological revolution that is bringing artificial intelligence and machine learning to Cenac’s old-school approach of watching the equipment like a hawk.
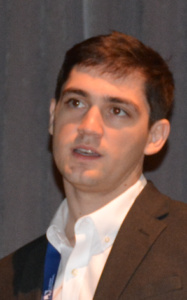
David Kober of IBA America spoke on the digital transformation of maintenance and repair. Doug Stewart photo.
The early generations of electromechanical monitoring have evolved to “systems that are starting to interact with each other without human intervention,” compiling constant systems monitoring, said Kober.Vessel operators are taking a strong interest in the technology, recognizing its predictive value, and wanting to adopt the latest, he said.
In that way, they are keeping out in front like the traditionalists.
Back in the 1990s Cenac began building his coolers with stainless steel, “because pitting behind those coolers is always an issue … it’s a little bit of an expensive project, but for 25 or 30 years you don’t have to worry about it.”
Training and paying crew to think of maintenance daily and other details to company culture make a difference too. Painting engine rooms white helps crews keep them clean and detect potential problems, and that attention to detail adds up, said Cenac.
“If those things are done, the drydock can save you two or three days of maintenance time and get that vessel back to work and producing revenue,” he said. “My philosophy was ‘do whatever you have to.’”
Too often, said Cenac, port captains tell shipyard managers, “well, I don’t have the budget for that.”
The response, he added, should be: “Well, go to your boss and get the budget.”