Small shipyards have always played an essential role in the U.S. maritime industry, often providing specialized services and craftsmanship that larger shipyards do not offer. However, staying competitive has become increasingly challenging. Yards must contend with regulatory pressures, inflation, supply chain issues, and a shrinking skilled workforce.
Multiple shipyard owners have emphasized the extensive regulations that their yards must follow to stay compliant, along with the costly need for legal and consulting support throughout the process. These regulations have been deemed by many as nonproductive and no longer just about building ships.
Yet, for these smaller shipyards, a crucial lifeline remains — the Small Shipyard Grant Program.
SCHOLARSHIP MONEY
Administered by the U.S. Maritime Administration (Marad), small shipyard grants have been a reliable resource for many shipyards across America, helping them modernize their facilities, purchase new equipment, and invest in workforce training. The program has also proved to be critical in maintaining the competitiveness of these smaller shipyards.
Given that, the survival and success of this program hasn’t always been guaranteed, and much of its continued relevance can be attributed to the efforts of the Small Shipyard Grant Coalition — a group formed to advocate for the program’s funding and support.
Dave Matsuda, a maritime industry veteran who served as Marad’s 17th maritime administrator, previously worked on Capitol Hill as a policy adviser and founded the coalition in an effort to help revive the program after Congress cut its funding in 2014 and 2015.
Having worked for Sen. Frank Lautenberg, D-N.J., who initially authored the legislation to create the program, Matsuda’s experience in both the legislative process and the maritime industry led him to develop the coalition, unifying shipyards and equipment manufacturers across the country. His efforts have been instrumental in keeping the Small Shipyard Grant Program alive, particularly during times when its funding was at risk. Sen. Tammy Baldwin, D-Wis., and Sen. Bill Cassidy, R-La., now lead the funding efforts in the Senate.
“When I left government, one of the staff at Marad said, ‘you know, you really ought to help those small shipyards, because nobody’s really helping them’,” Matsuda recalled.
The coalition’s efforts have helped secure millions of dollars in federal grants for small shipyards, allowing them to make critical upgrades that have, in many cases, transformed their operations.
UNDER THREAT
Now underfunded and under threat, the Small Shipyard Grant Program finds itself at a crossroads. For the past six years, Marad has offered around $20 million for the program. For example, in fiscal year 2023, 27 different shipyards across 20 states split a purse of $20.4 million to improve their facilities and upgrade their equipment.
But 2024 saw a steep cut to $8.75 million. “Even $20 million is a drop in the bucket in the scheme of the federal budget, but it has an outsized impact to the small shipyard industry,” Matsuda said.
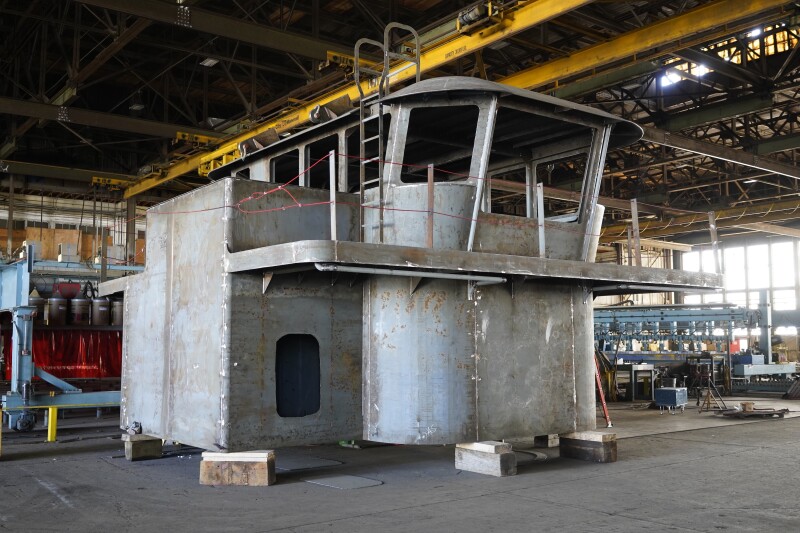
With the reduced funding, there are fewer grants and smaller awards, leading to a significant decrease in transformative projects like travel lifts and drydocks — essential elements for shipyard operations. This year, only one drydock was funded, and zero travel lifts, a sharp contrast to last year’s provision of four each. Matsuda notes that the shortfall is most telling in the absence of haul-out equipment, the backbone of any shipyard’s functionality, but he remains positive.
“This is a critical year,” he said. “If Congress comes back and gives us the 8.75 number again, we might be stuck at that for a while. And if they come back at 20, then it just kind of shows that [20]24 was an aberration, and that was just a onetime thing. We can go back to a funding level that’s more stable. It was funded every year, and it still is, so glad they didn’t cut it all together.”
The take home message from coalition-to-industry is that this is a critical time for the program. “If you care about this program, if you want to see it continue, you’ve got to be engaging with us, with your members of Congress, to let them know how important this is, and that we want to see the funding restored,” Matsuda said.
“We still come across folks who are new to the program or aren’t aware of the opportunities it provides,” he continued. “Our job is to keep spreading the word, helping shipyards secure the funding they need, and ensuring that this vital program continues to support the industry for years to come.”
BEST PRACTICES
Matsuda had never written a grant before starting this coalition. After one shipyard asked for assistance, he obliged, likening the process to writing a college term paper. “I spent two or three nights pulling late nighters. But we got the grant, and the next year I got smart and created a small team,” he said.
Over the years, Matsuda has developed a deeper understanding of what makes a grant application successful. “One of the unique things about this grant program is they require quantitative analysis, and I think generally grant writers have a hard time with that,”
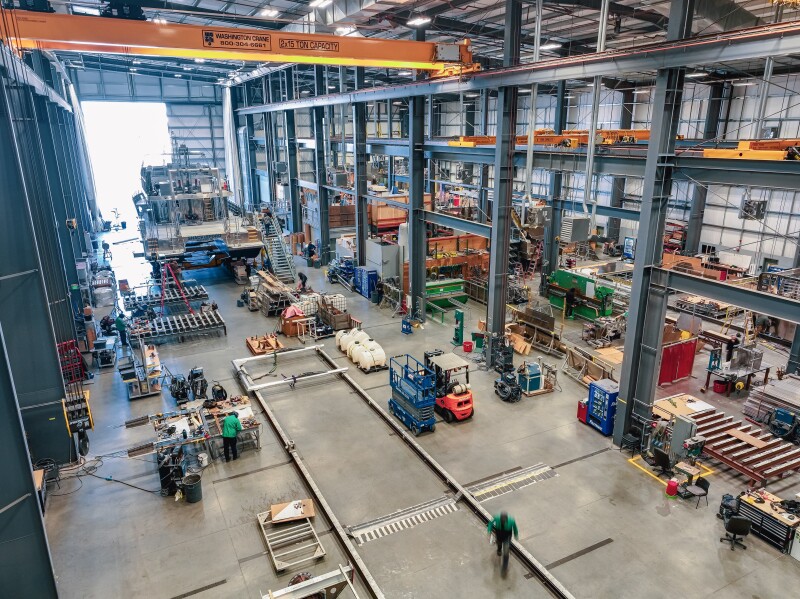
Marad is keen on funding training grants. Understandably, most shipyards apply for equipment; however, one way to have your application stick out is to include a training component. The Maritime Administration wants to see workforce development, Matsuda said, adding that many of the jobs created through the program are still around today. “This is not a jobs program, nor is it designed to be, but in effect, it is. It helps create and retain jobs long term. It helps companies grow,” he said.
As the program continues to evolve, the success stories of shipyards that have benefited from the grants are powerful testaments to its impact.
GRANT SUCCESS
Senesco Marine, North Kingstown, R.I., is currently working on two hybrid ferries bound for the Maine coast, and the final two-of-six WindServe Marine LLC crew transfer vessels (CTVs). The shipyard recently began work on a 140'x50' deck barge, which they are building on spec with the intent to sell or charter in the future. The deck barge construction marks a new development for Senesco, as it is advancing in the commercial barge industry and can build to suit any customer’s needs, the company noted.
Last year, Senesco was awarded a $738,289 grant through the Small Shipyard Grant Program to support the purchase and installation of a one-sided submerged arc welding system that consists of three integrated digital systems to load, fit, and weld multiple-plate panels, upgraded network servers and software, an all-terrain lift with variable reach, and a Tier 4 compressor.
“This machine runs a bead and can weld two (40'x40') plates together in about an hour and a half,” Ted Williams, Senesco Marine’s president, said in describing the benefits of that grant and the sub arc welder as an asset to the yard. “It would take a human about three-to-four days to do it,” he said, highlighting where the better part of the grant was allocated. Mike Foster, Senesco’s general manager, mentioned the increased capabilities that the new welding head will provide. “This one’s capable of welding up to five-eighths of an inch
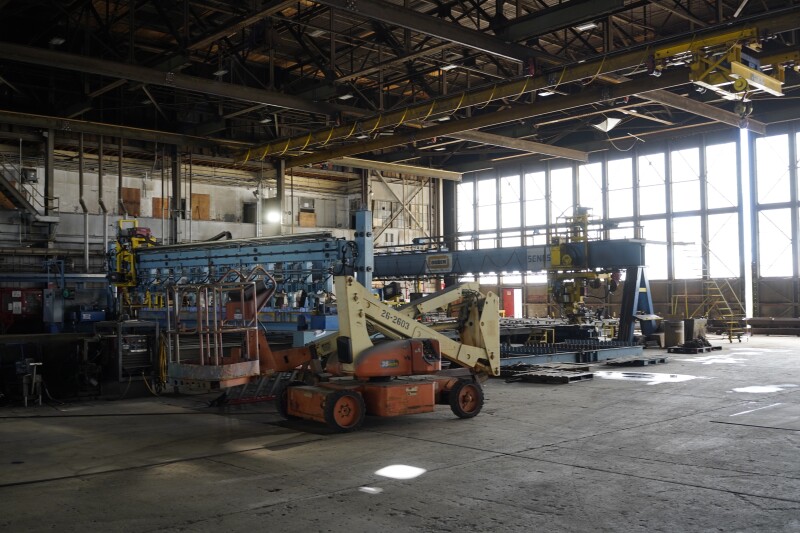
“Most importantly, we were awarded about half of a million dollars out of that grant to get a new head, that yellow head right there,” he said, pointing to the arc welder. “We’re going to replace that in a few months as that comes in. That’s an old analog system. We’re going to get a new digital system, which will make it even better, more accurate, and more refined.”
Williams emphasized the impact the Marad program has had since its inception. “That’s a great thing for shipyards to be able to tap into something like that and get that support.”
Further down the coast sits Colonna’s Shipyard, Norfolk, Va., a repair and refit yard that, next year, celebrates its 150th anniversary. The shipyard has received a number of grants through the program over the years, none more important than its 2008 grant that funded a new travel lift.
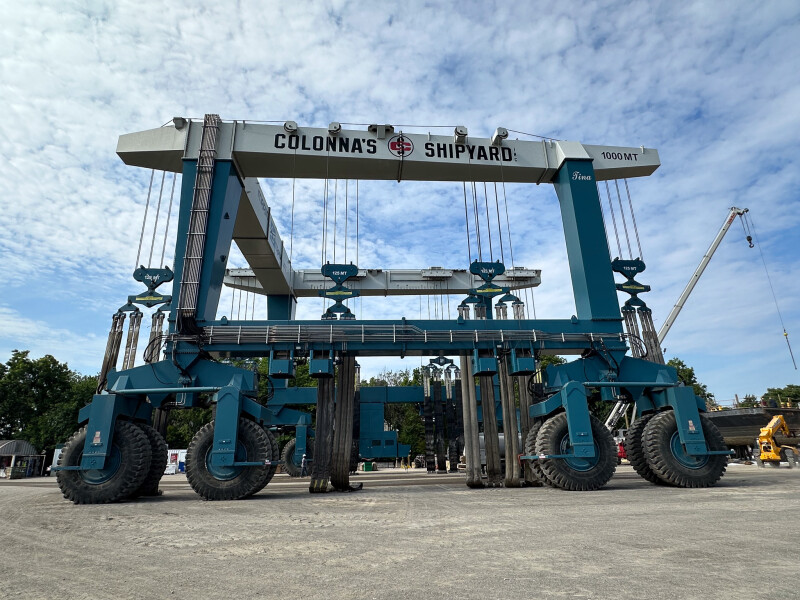
“Marine travel lifts are just transformative. Colonna’s is probably one of the best examples because of what they did. They were a yard that was limited to drydock or railway technology,” said Matsuda. “The travel lift is a force multiplier. All of a sudden, you’ve got six times, seven times, 10 times the amount of business.”
For a shipyard and industry what does that mean? For a lot of vessel owners, it means, they don’t have to travel as far out of their way to get service.
In 2017, Colonna’s was awarded $387,500 to support the purchase of a Link-Belt 110-ton rough-terrain crane. In 2020, the shipyard received $800,000 to purchase welding machines.
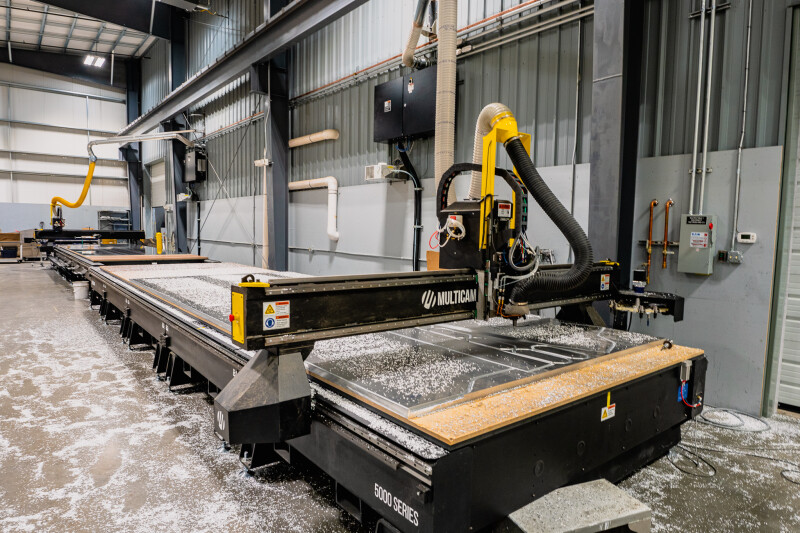
In 2023, All American Marine (AAM), Bellingham, Wash. was awarded $916,000 to purchase and install two 30' router tables and a CNC press brake. The shipyard recently delivered a 75'x27.5' patrol boat to the California Department of Fish and Wildlife. The yard is currently working on two research vessels, one headed to Cal Poly Humbolt and the other to the University of North Carolina, Wilmington. Also under construction is a Los Angeles port police boat, a 108' monohull, and a number of other vessels under contract.
“We went from one router to two, so it’s more than doubled our capacity, said Ron Wille, AAM’s president, “because if one’s tied up on a given job, we’re able to then use the other one. So, it’s been really helpful for us.”
It took some time for the staff to get properly trained on the new CNC press break, but it’s been worth the effort. “We already had an old CNC router, but what we didn’t have was a CNC press brake,” said Wille.
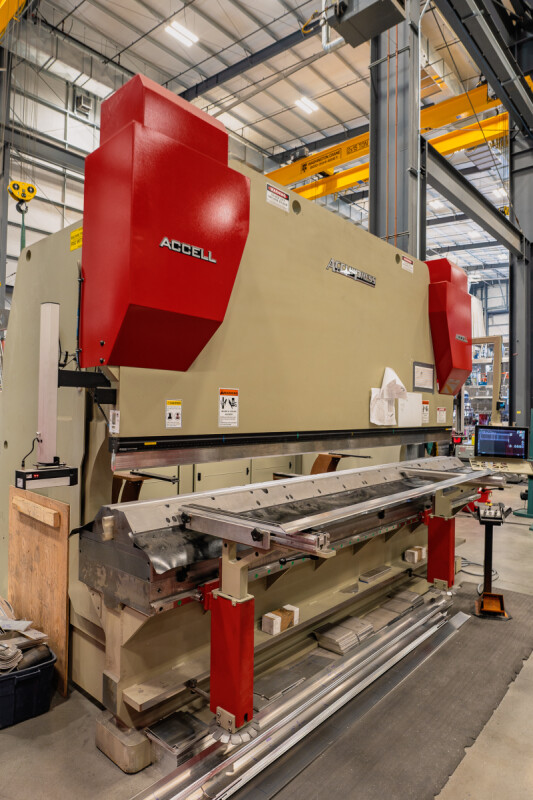
The new CNC press brake, with its 550-ton capacity, allows All American to handle heavy-duty forming tasks more efficiently and accurately. The ability to program the machine for repeat tasks has reduced production time and improved precision. The company’s previous press brake was manual and less efficient, especially for complex tasks like forming hydrofoils.
The new equipment has already been utilized in several projects, particularly those involving thick aluminum plates. “We build our own hydrofoils for a number of our projects,” said Wille. “In the years that we’ve been working with Teknicraft Design, it’s been 25 years now, we’ve built more than 75 Teknicraft-designed vessel hulls, and more than 40 of those boats have been equipped with a hydrofoil. That foil is a wing that spans between the two hulls.
“We are making those wings out of a much thicker plate now. Until we got this press brake, there were pieces of plate that we had to send to third parties to get formed because our machine was not powerful enough to actually bend aluminum that thick,” Wille continued. “And so, it’s pretty amazing to go out there now and watch this six, seven-foot piece of inch-and-a-half plate form up.”