Military patrol boats are used in a variety of different missions — coastal defense, maritime security, border control, anti-smuggling operations, counterterrorism, disaster relief, fishery patrols, law enforcement, search and rescue missions, and drug interdiction.
In all of these missions, the ability for a vessel to operate at high speeds and in any type of sea state is top of mind. What’s not often considered are the operators of these patrol boats, either first responders or military personnel, and the damage that running at high speeds in rough water can do to the human body.
PROJECT PERFECT STORM
At this year’s Multi-Agency Craft Conference (MACC) in Portsmouth, Va., put on by the American Society of Naval Engineers (ASNE), the gap between vessel design and operator safety was addressed in a presentation led by officials from Ocean Craft Marine (OCM). MACC is an open forum for the exchange of operational and technical information on small boats and craft between government agencies and the
“My father is a 100 percent disabled combat veteran who
Members of the innovative collaboration Project Perfect Storm brought OCM’s 11.5-meter (37.7') Offshore Interceptor to MACC, highlighting the project’s mission to build boats that exceed current standards for safety, comfort, and performance. The team emphasized the integration of technologies aimed at minimizing the impact of high-speed maneuvers and reducing G-forces on first responders and military personnel and addressing the lack of innovation on current military patrol boats.
The project’s multi-phased approach began with Phase 1 testing, a rigorous data collection of the vessel’s existing configuration, measuring shock impacts, accelerations, vessel pitch, and roll using up to a dozen Inertial Measurement Units (IMUs). These tests recorded G-forces up to 23 Gs at speeds of 60 miles per hour in challenging sea conditions. In Phase 2 testing, the vessel was stripped down, and a new streakless running surface was sculpted onto the aluminum hull for a second round of identical testing to compare results.
Phase 3 of the project included the addition of the Porta Products Hydraulic Transom Lift System for additional data collection, followed by phase 4, which included the addition of the Seakeeper Ride system. Additional phases will include a collaborative effort of over 15 companies from the maritime industry, showing how competition was set aside to achieve a common industry wide maritime goal.
The integration of various technologies from all the Project Perfect Storm partners aims to create the ultimate highspeed pursuit vessel, combining safety, speed, and cutting-edge technologies. The cooperation serves as a model for future industry projects, demonstrating the potential of united efforts in advancing maritime capabilities. The various companies involved include Ullman Dynamics, Sharrow Marine, Skydex, Military Systems Group, and Hefring Marine, resulting in features like shock mitigating seats, articulated weapon mounts, shock-absorbing deck pads, a reconfigurable deck layout, and AI-based optimal routing technology.
Todd Salus, co-founder and vice president of OCM, detailed the Offshore Interceptor’s working deck space, twin diver notches, and specialized shock-mitigating seats that ensure operator comfort and safety. Salus also emphasized the importance of data collection and collaboration, inviting new partners to join the project.
“We’re here to collect as much data as we can, and then give it all away for anybody to use. I’m not doing this to sell boats. I want to offer this as a legacy project to protect future operators,” said Salus.
Scott Porta, owner of Porta Performance, was heavily involved in the hull reconfiguration of the vessel. Porta holds 11 world and national offshore points championship titles in the APBA Super Stock Catamaran offshore racing class. “I’ve been in this stuff since I was a kid, and I absolutely love making things work better and go faster,” he said. Porta Performance also provided the hydraulic transom lift system for the project.
Porta spoke about the advancements in technology being used to measure efficiency in Project Perfect Storm, making mention of his old method of hanging over a boat’s transom traveling at 100 mph. “The technology that I’m hooked up with, with these guys (Project Perfect Storm), is just phenomenal. And for a change, I’m looking up. I’m looking at other people that have educated themselves tremendously.”
Keith Hubble, principal engineer at TMS Group, provided data on the OCM Offshore Interceptor’s performance, showing significant reductions in vertical, lateral, and forward accelerations due to the technologies employed. This model of the stabilizer system is a prototype for larger vessel applications. The Seakeeper Ride system was tested in various sea conditions, which demonstrated control over vessel roll and pitch, leading to a more efficient, smoother, and safer ride for all onboard. The combined technologies on the modified vessel resulted in a 26% to 77% reduction in vertical accelerations, in various sea conditions, and compared to stock configurations. All of these improvements to the boat’s ride, comfort, safety, reduced operator fatigue, and situational awareness are known in the industry as “Human Factors.”
The presentation concluded with a message about the potential impact of such advancements, suggesting that if these technologies had been available 20 years ago, many injuries and disabilities among patrol boat operators could and would have been prevented.
The team at Project Perfect Storm will be presenting their project’s results in an educational session at this year’s International WorkBoat Show in New Orleans this November.
In a follow-up discussion, Ryan Salus reflected on the current trends in military patrol boats and the pressing need for innovation. “A lot of what the Navy and the Coast Guard are buying are larger aluminum boats. So that’s why we’re really pushing the innovation on the aluminum side... And that’s kind of where the seed for Project Perfect Storm came about. Everyone was kind of staying in their competitive silos, and they’re not really innovating their hull forms. And operators are continuing to get beat up out there. So that’s why our focus is really pushing the innovation of getting aluminum hull forms up to speed to where they’re just as good (as fiberglass).”
OLD PROS
Exhibitors Silver Ships, Theodore, Ala., and Louisiana boatbuilder Metal Shark are prolific patrol boat builders, and they are both building now.
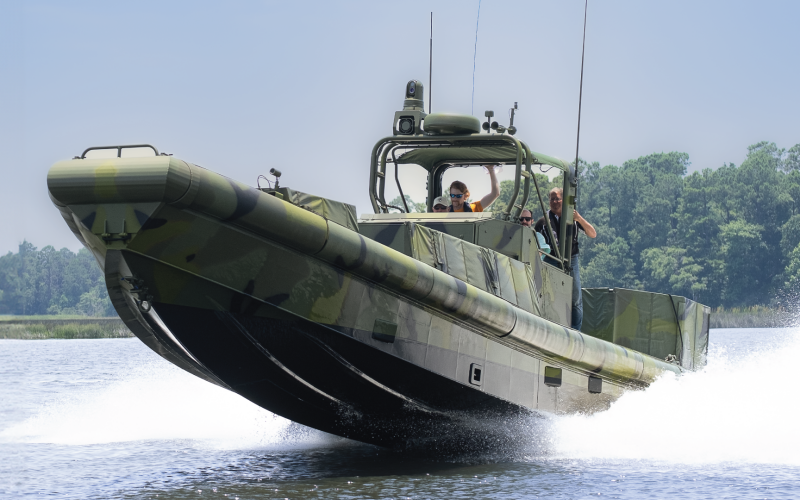
Silver Ships delivered six riverine patrol boats (RPB) this past October under a contract award worth $6.12 million from the Naval Sea Systems Command. The vessels were designed and constructed as a part of the U.S. Navy Foreign Military Sale (FMS) program and will benefit an unnamed Pacific region ally. The six 40'6"x10.7'x2' center-console patrol boats are powered by twin Yanmar 6LY2A-STP engines generating 440 hp at 3,300 rpm connected to Hamiltonjet HJ-292 waterjets. The boats use Livorsi controls
In April 2024, under the same FMS program contract, Silver Ships delivered the first four coastal fast response boats (CFRB) which will benefit the NATO Navy. The other three boats currently under construction will support an unnamed Central American navy upon delivery. The seven custom designed 43'x12'6"x3' military CRFBs will feature a cabin and WING collar system. The boats are powered by twin Caterpillar C7.1 inboard diesel engines producing 500 hp at 2,900 rpm that
Ship’s service power comes from MEPS 240-volt, 50-Hz generators.
The electronics suite is largely made up of Furuno equipment but also features a FLIR M364, Rhotheta direction finder, Motorola encrypted radios, and Zipwake dynamic stabilization system.
“The Silver Ships 43-foot coastal fast response boat is a highly versatile, coastal patrol boat capable of fulfilling multiple missions, such as harbor defense, warship force protection, counter narcotics operations, maritime interception operations, search and rescue, medical evacuation, humanitarian assistance, among other roles,” said Capt. Shawn W. Lobree (retired), who is Silver Ships’ federal program director. “The boat has a robust, deep V hull form with a well-equipped cabin and can operate in coastal and offshore waters for several days at a time, if needed.”
Both the RPB and CRFB patrol boats were designed inhouse by the shipyard’s Clay Danielson and Ben Bates.
Also exhibiting at MACC 2024 was La.-based boatbuilder Metal Shark, who, in conjunction with ReconCraft, Clackamas, Ore., was awarded a seven-year U.S. Navy indefinite delivery/ indefinite quantity (IDIQ) contract worth up to $290 million to produce
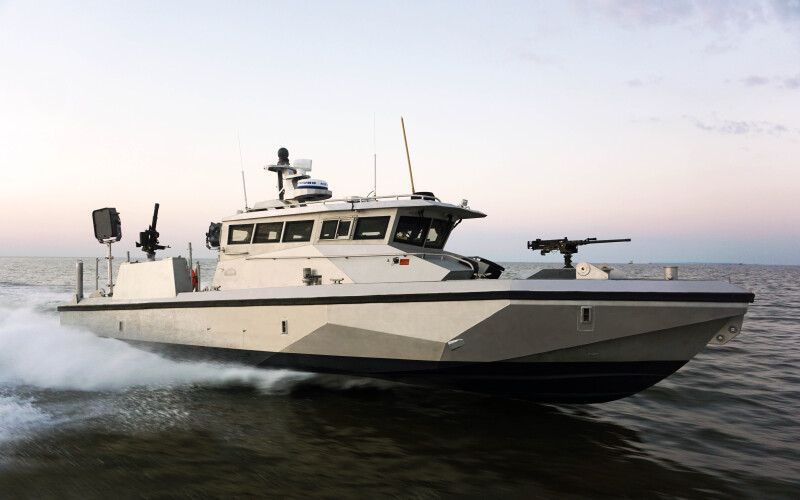
Metal Shark continues to build 14 40 PB vessels under the original 40 PB Flight 1 IDIQ, with a total of 42 boats delivered to date. With the award of Flight 2, the Navy has placed an initial, immediate order for two additional vessels from Metal Shark, which will be delivered in 2025. Under the terms of the award, Metal Shark will supply spares, training, engineering, and technical support in addition to the vessels.
The 40 PBs are ballistic-protected combatant craft powered by twin diesel inboards and waterjets containing a chiseled, angular profile and a unique faceted hull.
Designed by Metal Shark’s in-house engineering team specifically for the Navy, the 40 PB has been built by Metal Shark since award of the 40 PB Flight
1 contract in 2017. With the Flight 2 award, 40 PB production will continue in force at Metal Shark’s South Louisiana production facilities, with ReconCraft also building at its Clackamas, Ore., facility.
“Winning 40 PB Flight 2 is a huge win for the entire Metal Shark family, our suppliers, and the state of Louisiana,” Metal Shark CEO Chris Allard said in a statement announcing the contract. “We have developed our processes, built our facilities, and grown and trained our team specifically to accommodate high volume, rapid and repeatable, high quality, serialized construction of complex vessels like 40 PB. With the award of Flight 2, we will continue to showcase the skills of our Louisiana workforce while supplying these important combatant craft to our fighting forces.”
Metal Shark engineers designed the 40 PB with a moderate aft deadrise, wide waterplane, and sharp entry hull form that helps them achieve 35+ knot sprint speeds while displaying dynamic stability in a range of conditions,” according to the company.
The design “also offers enhanced handling and greatly reduced operating cost at the 10-15-knot escort and cruise speeds where the vessel spends the bulk of its operational life. The 40 PB features a C4ISR suite and can be armed with a range of crew-served and remotely operated weapons systems,” company officials said.
“Winning 40 PB in 2017 was a crowning achievement for Metal Shark, and we are equally honored to have received this Flight 2 award as evidence of the Navy’s continued trust in us today,” said Allard. “As a vital part of the defense industrial base, Metal Shark proudly supports those who serve and protect. We are excited to continue supplying the world’s greatest Navy with the world’s most advanced patrol boat.”
ASNE is a professional engineering society for engineers, scientists and allied professionals who conceive, design, develop, test, construct, outfit, operate and maintain complex naval and maritime ships, submarines and aircraft and their associated systems and subsystems. ASNE also serves the educators who train the professionals, researchers who develop related technology, and students who are preparing for the profession. Society activities provide support for the U.S. Navy; U.S. Coast Guard; U.S. Marine Corps; U.S. Merchant Marine and U.S. Army.
The group is the seventh oldest technical society in the U.S. It was founded in 1888 by a group of officers of the U.S. Navy's Engineering Corps.